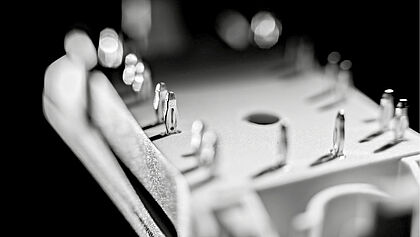
Vincotech's Press-fit technology reduces PCB assembly time and effort considerably. Well established in the automotive industry, the Press-fit pin eliminates the need for soldering. This cuts process time and costs, and boosts production output capacity. With no need to solder modules, engineers enjoy great flexibility in design. The module can easily be mounted on top or bottom of the PCB at no extra cost and effort.
Benefits
- Eliminates costly additional soldering
- Pins are in the same position as solder pins
- High current carrying capability (30 A @ 80 °C)
- Flexible mounting onto the power module DCB
- Cuts production costs
- Reliable cold-welding connection to PCB
- No PCB hole damage to enable reuse
- Thermo-mechanical push and pull force relief
Features
- Approved rounded Press-fit area
- Complies with DIN and IEC standards
- Tapered pin head
- Available for almost all housings
- Application Note: Vincotech's Press-fit Pin
- Video: Press-fit technology - the new interconnection technology
- Video: Press-in process with flow 1B housing
Press-fit pin
Press-fit pins forge a solid bond between two parts that requires no additional soldering. Frictional force holds the parts together after they have been joined to create a gas-tight, cold-welded, solder-less connection.
Press-fit pins emerged in the early 1970s. The DIN 41611-5 standard for this technology was first published in 1984, and the IEC guidance 60352-5, "Solder-less connections – Part 5: Press-in connections – General requirements, test methods and practical guidance,” soon followed. Components that meet these qualifications are called 'compliant,' and the term 'compliant pin' is widely used throughout the market.
Engineers started replacing soldered pins and screws with these alternatives in the mid-1980s, and modules equipped with these pins debuted in 2005.
Today these pins come in various sizes and shapes, one of the most common being the eye-of-the-needle, or Press-fit, pin. Its ability to stand up to vibrations prompted automakers to use it for diesel engines.
Figure 1 shows an improved eye-of-the-needle Press fit pin which was patented and has been used in Vincotech modules since 2008. Follow the links to learn more about European, German and US patents.
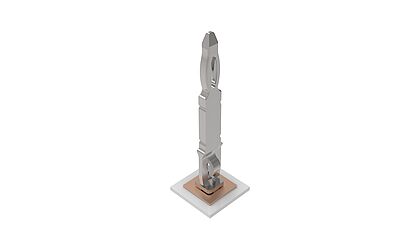
The pin is made of a copper alloy with nickel plating and a tin finish. Every Vincotech pin comes with an s-bend at the bottom to provide stress relief. It facilitates assembly and may be pushed or pulled as needed for a pre-bent DCB or baseplate. This stress-relief also offsets heat- and cold-induced expansion and contraction.
Property |
Value |
Unit |
---|---|---|
Underplating |
Ni |
|
Surface of pin |
Tin |
|
Recommended PCB finish |
I-Sn |
|
Alternative PCB finish |
HA(S)L / NiAg |
|
Current carrying capability @ ∆T = 25 K |
30* |
A |
Thermal conductivity λ |
320 |
W/mK |
Thermal capacity c |
381 |
J/kgK |
Thermal expansion coefficient α |
17.6 |
1-06/K |
Density ρ |
8.92 |
g/cm³ |
* Depending on PCB layout